ティエムファクトリ株式会社
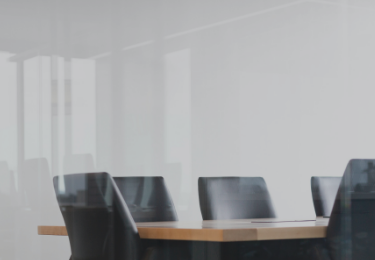
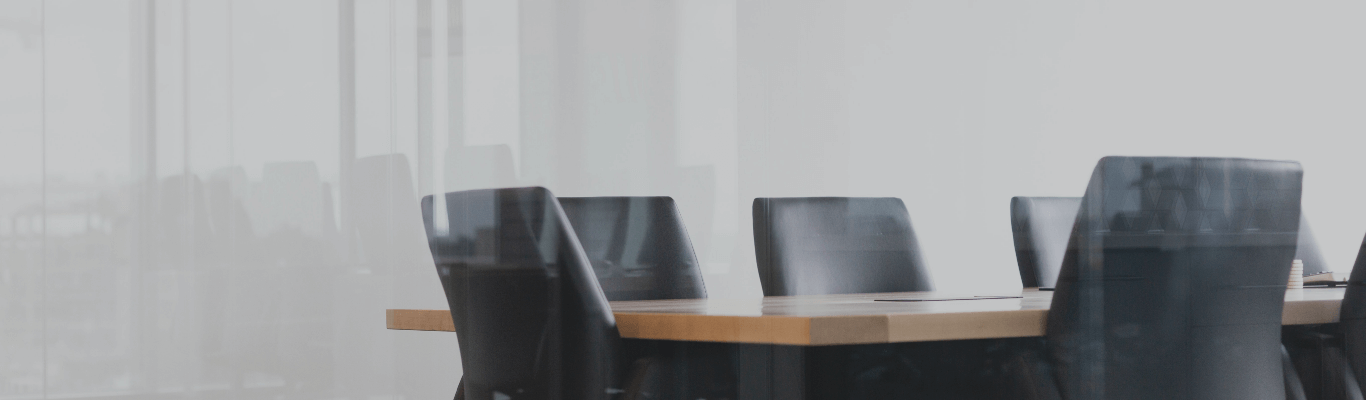
ティエムファクトリ株式会社
新素材で世界に光と、ぬくもりを。
ティエムファクトリは京都大学との共同研究の結果、現実的なコストで板状(モノリス)エアロゲルを生産できる技術を発明することに成功し、これをSUFA(=Super Functional Air)と名付けました。モノリスタイプでなければ透明性を維持することは難しく、そのためSUFAの量産化に成功すれば、世界初の透明断熱材サプライヤーとなります。世界初の透明断熱材メーカーとして「SUFA」を世の中に提供することで、光を透し温もりを守る「窓」を再発明するとともに、他の材料と複合化し、建材、自動車、物流といった身近なシーンへ幅広く普及させていくことを目指しています。
SUFAは、世界で最も使われている断熱材(グラスウール)の約3倍の断熱性能を持っています。つまり従来の断熱性能を実現するための断熱材の厚さが1/3で済むため、透明である特徴を抜きにしても、既存の断熱材料に比べて住空間や輸送機などへの実装で大きなメリットを発揮します。
慶応義塾大学にて博士号を取得したのち、複数の国立研究機関でポストドクターとして様々な研究に従事してきました。その中で、個人的に優れた研究成果を創り上げていくだけでなく、それを具体的に人類のために役立つようなカタチにしたい、という想いが強くなるのを感じておりました。そして社会人研究員として京都大学に在籍していた時に、同じ京都大学の研究成果として研究室に眠っていたエアロゲル(SUFAのもととなった断熱材)と出会い、「この素材を世界中に広めることで人類に貢献したい」という衝動にかられ、起業するに至りました。
弊社のSUFAは製造過程において危険物であるアルコール類を取り扱う必要があり、事業化を進める上でこれが予想外に大きなハードルとなりました。設立間もないベンチャーはインキュベーション施設のラボを使うことになりますが、大抵の施設では扱える危険物の数量がごく僅かに設定されています。そのため、ある程度の規模の自社ラボを建てなければ、研究開発すらままならないということが判明しました。しかしその一方で、その費用を賄えるだけの資金を調達するためには、そうした制約の中でも研究開発を進め、しっかりと企業価値を向上させる必要があります。
企業価値の向上と資金調達を繰り返すことで、少しずつ事業を進めてきたため、ここまでたどり着くのに時間を要してしまいましたが、おかげさまで2020年4月にようやく茨城県に自社ラボを建設することができ、事業化に向けて必要なインフラがようやく整ってまいりました。
SUFAは世界初の透明断熱材であり、様々な用途で実用化することで人類のCO2排出量を10%削減する、という大きなミッションを当社として掲げております。そのためには、単に断熱材として販売するだけでなく、企業やコンシューマーに対して様々な「断熱ソリューション」を提供していくことが求められます。というのも、市場に流通する断熱材には十分なバリエーションがないなどの理由により、適切な形で自社製品の断熱ができている企業は少なく、さらにSUFAのような新規材料は扱いが難しいため、単に素材として販売してもなかなか製品への搭載まで進みません。そこでSUFAを他材料と複合化し、使いやすい形にして提供する、または相手先企業の持つ原料との複合化を共同で開発するなど、断熱に関するペインを解消していく必要があります。さらにコンシューマーから見ると、適切な断熱により得られる価値は「心地よさ」ですので、ブランドの認知向上という観点から、これを体感できる最終製品を販売していくことも視野に入れていきたいと考えております。世界中の建物やモビリティ、電化製品などにSUFAが搭載される未来に向けて最適な断熱ソリューションを提案する、これが当社の提供していく価値です。